A Comprehensive Guide to the Refine and Advantages of Plastic Extrusion
In the vast world of manufacturing, plastic extrusion becomes a extremely reliable and crucial procedure. Altering raw plastic into continuous accounts, it caters to a variety of sectors with its exceptional flexibility. This guide intends to illuminate the intricate actions included in this method, the kinds of plastic proper for extrusion, and the game-changing advantages it offers the industry. The taking place discussion guarantees to unfold the real-world impacts of this transformative procedure.
Comprehending the Essentials of Plastic Extrusion
While it may appear complex at initial glance, the procedure of plastic extrusion is basically basic - plastic extrusion. It is a high-volume production technique in which raw plastic is thawed and formed right into a continual account. The procedure begins with the feeding of plastic material, in the form of powders, pellets, or granules, into a heated barrel. The plastic is then melted making use of a combination of warmth and shear, applied by a turning screw. Once the molten plastic reaches completion of the barrel, it is forced through a little opening referred to as a die, forming it right into a preferred form. The shaped plastic is then cooled, strengthened, and reduced right into preferred sizes, completing the procedure.
The Technical Refine of Plastic Extrusion Explained
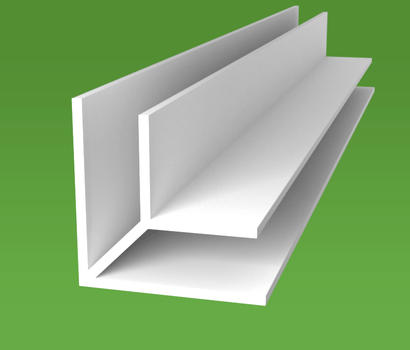
Sorts Of Plastic Suitable for Extrusion
The selection of the appropriate sort of plastic is an important facet of the extrusion procedure. Different plastics supply one-of-a-kind residential or commercial properties, making them a lot more matched to specific applications. Polyethylene, as an example, is generally utilized because of its inexpensive and simple formability. It provides exceptional resistance to chemicals and dampness, making it excellent for products like tubes and containers. Polypropylene is one more preferred option due to its high melting point and resistance to tiredness. For even more robust applications, polystyrene and PVC (polyvinyl chloride) are frequently picked for their stamina and longevity. Although these prevail choices, the choice eventually relies on the certain demands of the item being generated. So, recognizing these plastic kinds can substantially boost the extrusion process.
Contrasting Plastic Extrusion to Various Other Plastic Forming Approaches
Understanding the kinds of plastic ideal for extrusion paves the way for a wider discussion on how plastic extrusion piles up versus other plastic developing techniques. Plastic extrusion is exceptional when it comes to creating constant profiles, such as gaskets, pipes, and seals. It likewise permits for a regular cross-section along the size of the item.
Secret Advantages of Plastic Extrusion in Manufacturing
In the realm of production, plastic extrusion provides numerous considerable advantages. One remarkable benefit is the cost-effectiveness of the procedure, that makes it a financially attractive manufacturing technique. Furthermore, this method supplies remarkable item versatility and improved manufacturing rate, therefore raising total manufacturing effectiveness.
Cost-Effective Production Technique
Plastic extrusion jumps to the forefront as an affordable production technique in manufacturing. This process stands out for its click to find out more ability to generate high volumes of product promptly and effectively, offering manufacturers with substantial cost savings. The main cost benefit is the ability to make use of much less expensive basic materials. Extrusion utilizes polycarbonate materials, which are much less pricey contrasted to metals or ceramics. Further, the extrusion process itself is fairly simple, lowering labor expenses. In addition, plastic extrusion requires much less power than conventional production methods, adding to reduced operational expenses. The procedure also lessens waste, as any defective or excess products can be reused and reused, offering an additional layer of cost-effectiveness. In general, the economic advantages make plastic extrusion an extremely eye-catching option in the manufacturing market.

Superior Product Flexibility
Beyond the cost-effectiveness of plastic extrusion, another significant benefit in making hinge on its premium item adaptability. This procedure enables the production of a vast variety of products with varying shapes, dimensions, and layouts, from straightforward plastic sheets to detailed profiles. The flexibility is connected to the extrusion pass away, which can be personalized to yield the wanted item design. This makes plastic extrusion an excellent remedy for sectors that need customized plastic components, such as vehicle, building, and packaging. The capacity to create diverse products is not only helpful in conference particular market needs but additionally in allowing manufacturers to discover new line of product with minimal capital expense. Fundamentally, plastic extrusion's product versatility cultivates advancement while enhancing functional performance.
Improved Production Speed
A substantial advantage of plastic extrusion lies in its enhanced manufacturing rate. Couple of other manufacturing processes can match the speed of plastic extrusion. In addition, the capacity to keep regular high-speed manufacturing without compromising product quality sets plastic extrusion apart from various other methods.
Real-world Applications and Impacts of Plastic Extrusion
In the world of production, the method of plastic extrusion holds extensive value. This procedure is commonly made use of in the production of a variety of items, such as plastic tubes, window frameworks, and weather condition stripping. Therefore, it substantially influences sectors like building and construction, packaging, and auto markets. Furthermore, its influence prolongs to day-to-day products, from plastic bags to toothbrushes and disposable flatware. The economic advantage of plastic extrusion, mostly its cost-efficient and high-volume output, has actually changed manufacturing. Nonetheless, the environmental effect of plastic waste continues to be a worry. As a result, the industry is persistently striving for advancements in recyclable and biodegradable products, indicating a future where the benefits of plastic extrusion can be preserved without jeopardizing ecological sustainability. read this article
Conclusion
Finally, plastic extrusion is a effective and highly efficient method of transforming basic materials into varied products. It uses many benefits over various other plastic forming methods, including cost-effectiveness, high result, marginal waste, and design flexibility. Its effect is greatly really felt in various industries such as construction, vehicle, and customer products, making it a critical procedure in today's manufacturing landscape.
Digging much deeper right into the technical process of plastic extrusion, it begins with the selection of the suitable plastic product. As soon as cooled, the plastic is reduced right into the needed lengths or wound onto directory reels if the item is a plastic movie or sheet - plastic extrusion. Contrasting Plastic Extrusion to Other Plastic Forming Approaches
Recognizing the types of plastic suitable for extrusion paves the method for a more comprehensive discussion on exactly how plastic extrusion stacks up against various other plastic developing approaches. Couple of other production processes can match the rate of plastic extrusion.
Comments on “Understand the versatility of plastic extrusion in design”